Also wrong about manufacturing costs. Hand soldering is THE most expensive operation in electronics manufacturing. The labor costs for the hard wiring are way more than the cost of a connector.
This is starting to be funny.
Normally I would have dropped out of this discussion, but I got zapped by a ray yesterday and my foot is really sore and I can't sleep, so I am going to contine.
I think you have come to the realization that the conductors have to be connected to the board...and it is inconsequential whether those conductors come from a removable connection on the bulkhead of the detector...or are the wires coming directly from the coil or headphones. (Incidentally, the wires do not have to be soldered to the board at all. They can be plugged into the board, for instance. They can be fastened to pins on the board with a zip gun. They can even be screwed or bolted to the board...as you can see on the small board behind my Sea Hunter's ikelite connector).
Anyway, to illustrate what an industry standard waterproof "through-hull" or "wire pass through" or "hard wired" fitting actually looks like, here are the fittings on the bulkhead of my White's BHID:
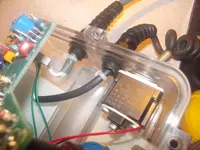
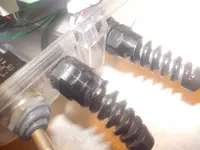
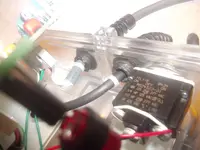
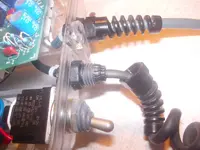
Mounting one of these fittings is no more difficult than mounting a removable connector. In fact, it is easier. There is no soldering involved. You can probably get the idea from the pictures, but I will run down the steps:
The male threaded fitting is placed through one of the holes in the housing and is affixed to the housing chenically or thermally or possibly a combination. On some fitings, there is a "backing nut" behind the male fitting that provides mechanical support.
The coil or headphone wire is threaded through the female or stress releaving fitting (the squiggly part).
The wire is run through the male threaded fitting with enough length to arrive at the PC board and whatever connectors that are going to be used (if any).
The female fitting is tightend down on the male fitting and the pressure exerted by this tightening action compresses the flanges at the top of the male fitting providing a waterproof seal on the wire.
Depending on the rating of the fitting, silicone is sometimes injected into the fitting, mostly as a saftey measure.
A wire tie is placed between the board and the fitting to releive potential pressure on the wire and to keep it from being pulled out.
That's it. Done deal.
Incidentally, I think a fitting of this type wholesales for about .12 cents
By way of comparison, an Ikelite male and female retail for around $40.00.
A manufacturer who bought them by the thousands could probabaly lower this price substantially, but in any case, it would still cost a hell of a lot more than .12 cents.
Now please explain to me how a manufacturer could attach an Ikelite type female connector to the detector housing, wire the female Ikelite connector to the circuit board...and then atttach a male Ikelite fitting to the headphone or coil wire...and do all this more cheaply than the hardwired example I have just showed...